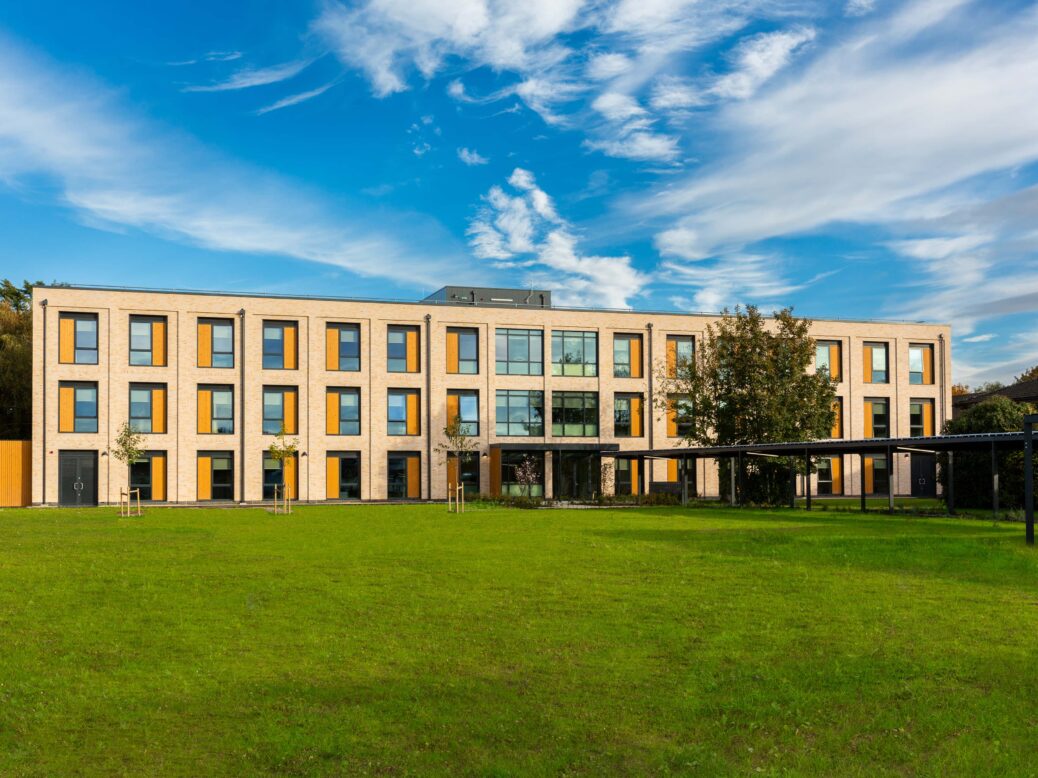
If there’s one issue everyone can seemingly agree on, it’s that the UK has a severe housing crisis, following decades of under supply.
Labour is right to put building more homes at the centre of its programme for government and action to speed up the moribund planning system will certainly help. But reforming planning alone will not resolve the crisis, because the construction industry simply does not have the labour force necessary to deliver the increase in homes required. This is not a new problem. The skills crisis in construction goes back many years, predating Brexit, which only exacerbated the issue. To truly resolve this crisis, we need to look at the way the construction industry builds homes.
It is often said that construction has let the industrial and technological revolution pass it by. Just look at the advances made in car manufacturing in recent decades, with the introduction of robotics and now AI, and compare that to housebuilding, where in many ways homes are still being built as they were 100 years ago: with contractors laying bricks in muddy fields.
But technologies to modernise construction do exist. At Reds10 we have been pioneering them for more than a decade now, developing highly sustainable, innovative, high-quality modular buildings offsite in our dedicated factories in Driffield, East Yorkshire, for the public sector. These include amazing homes for the military, school buildings and facilities for the Ministry of Justice and the NHS.
However, in the UK, this process, known as Modern Methods of Construction or MMC, has yet to enter the mainstream. This is at least in part due to the nature of our housebuilding market, dominated as it is by a small number of large housebuilders, who have a near monopoly over the market and therefore little incentive to drive forward innovation.
In the UK modular construction has also suffered from a perception problem – a hangover from poorly constructed post-war prefabricated buildings. This perception is grossly outdated: a bit like comparing a Morris Marina with a Tesla. Take, for example, our award-winning Imjin Barracks project, which provides modern accommodation for Army personnel based at the Headquarters of the Allied Rapid Reaction Corps in Gloucestershire. This highly sustainable three-storey building comprises 69 single en suite bedrooms, alongside communal living and dining facilities, kitchens, drying rooms and utility rooms.
The innovative building not only provides the UK’s defence personnel with modern and comfortable accommodation but is one of Europe’s most advanced ‘smart’ buildings, generating and analysing 21,000 data points (including humidity, door and window contacts, sound levels, temperature, daylight, power metering, water and more). This ensures the building’s performance can be optimised in real time, allowing for significant energy and cost savings.
Built offsite through our advanced construction techniques, Imjin Barracks, like all the projects Reds10 delivers, is unrecognizable from the much-maligned ‘prefabs’ of yesteryear and is indistinguishable from buildings built through traditional construction techniques.
What does distinguish our buildings from those built through traditional construction techniques, however, is the quality, the high sustainability credentials, and the speed and efficiency of the building process. These benefits are achieved through the advanced construction techniques that we deliver in our factory environment, which has the capacity to deliver 4,000 units per year.
Our factory production process is optimised for efficiency using repeatable processes and components, modern manufacturing tools, and advanced technologies that would be impractical on a construction site. The efficiency of factory construction means project delivery time scales can be drastically reduced by up to 50 per cent.
The efficiency of MMC also means that we can build projects with less labour. Across our pipeline we use around 30 per cent less labour than would be required by traditional construction techniques. We think that this can be reduced further as we move to greater levels of automation and industrialisation. If construction as a whole industrialised in this way, the skills gap could be bridged, helping the industry deliver the buildings and infrastructure the country needs.
Industrialised construction also greatly improves quality, with fewer post-construction snagging issues. Buildings are more airtight, providing greater energy efficiency without additional cost. Indeed, under our Carbon Negative at Zero Cost initiative, Reds10 ensures all its buildings are designed and built to operate at net zero, with the lowest possible embodied carbon – at no extra cost to the customer. And with around 90 per cent of the construction completed in the factory, there is also far less disruption to local communities from works on site.
There are further benefits that go beyond the sustainability, quality, efficiency, speed of delivery and lower cost of the buildings themselves. In our factory settings we employ our own workforce, investing in their skills and career development and supporting young people into apprenticeships and training opportunities. By other industry standards this may seem unremarkable, but within construction, it is increasingly rare. This is because the industry is dominated by a business model that sees a main contractor managing an ever-growing chain of smaller suppliers, rather than employing their own workforce.
This model is inefficient, drags down productivity, and fails to incentivise investment in skills and innovation – and it means that despite decades of technological advances, this has not flowed through to improved productivity in the construction industry.
Ultimately, MMC and the benefits it brings have huge potential to transform the construction industry and the way we build homes in this country, providing better quality, more efficiency, greater cost reductions, higher productivity, and improved sustainability. And we could do that with a smaller workforce, helping overcome the skills crisis that is currently holding back the industry delivering what the country needs.
At Reds10, we are actively developing prototypes that take what we have learnt from building innovative and high-quality housing for the defence forces – projects like Imjin Barracks – and applying that to the delivery of social housing. This is the next step in the evolution of MMC; moving it into the mainstream so that the benefits can be scaled, bringing housebuilding into the 21st century, helping tackle the housing crisis and providing a sustainable future for our country.
This article first appeared in our Spotlight Housing supplement, published on 29 November 2024.