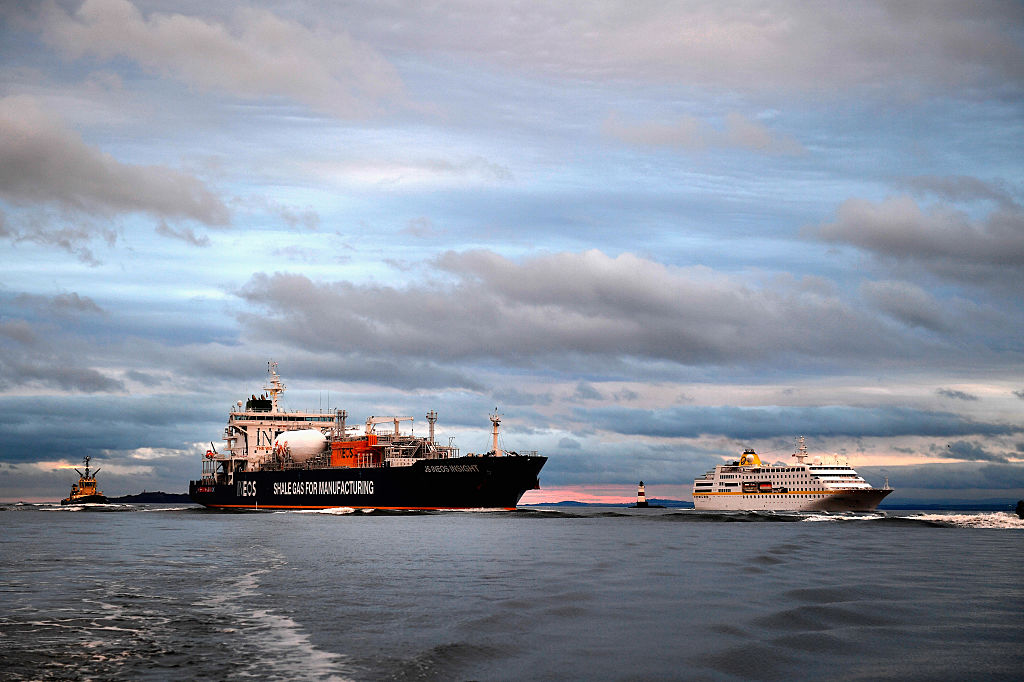
When he finished school Allan Dickson wanted to continue studying, but the prospect of student debt put him on an unconventional path.
“My guidance teacher gave me a book called sponsorship for students, and it was basically a big list of companies that would sponsor somebody to go to college or university,” he recalls.