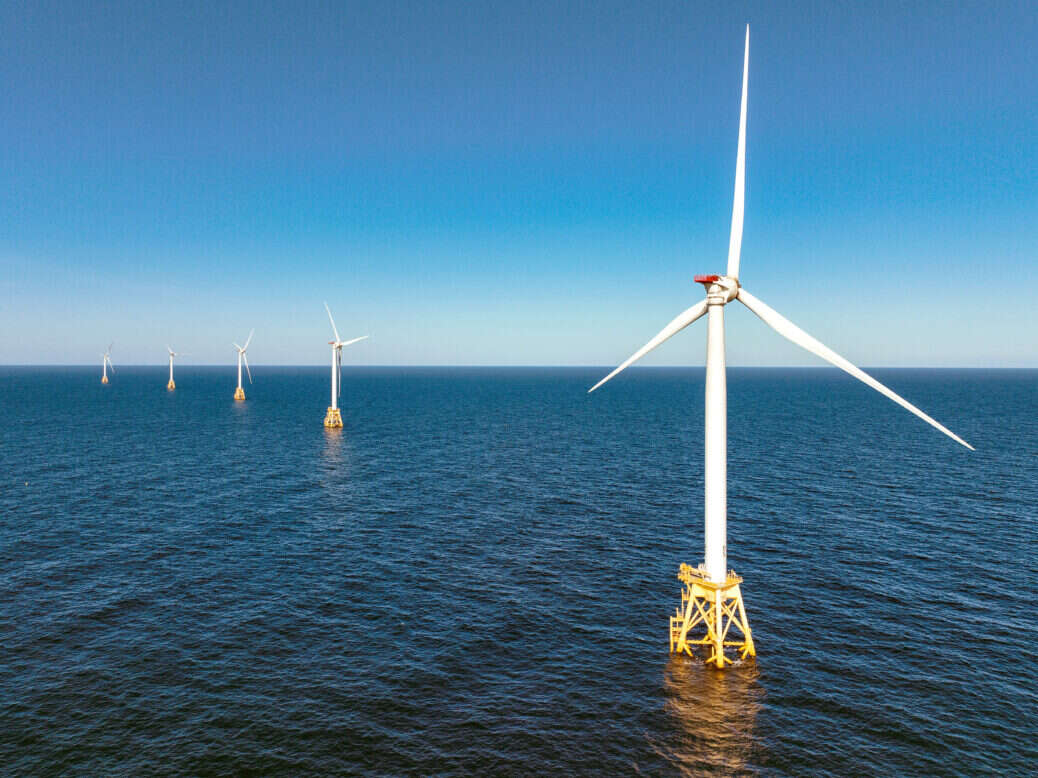
Soaring energy prices this year have led to record-breaking profits in the oil sector. Just this week, BP announced that its underlying profits between April and June had more than trebled compared to last year. Still, analysts are maintaining that big oil is living on borrowed time. More than 90 per cent of the world’s economy is committed to net zero, and even if it is not yet happening fast enough, these pledges mean that policymakers everywhere are planning how they can rapidly phase out fossil fuels.
The UK currently generates around 45 per cent of its electricity from fossil fuels. But plans are in place to move from generating 55 per cent low carbon power today, to 95 per cent low carbon power by 2030. This is a mammoth undertaking that will involve billions of pounds of investment in renewables.