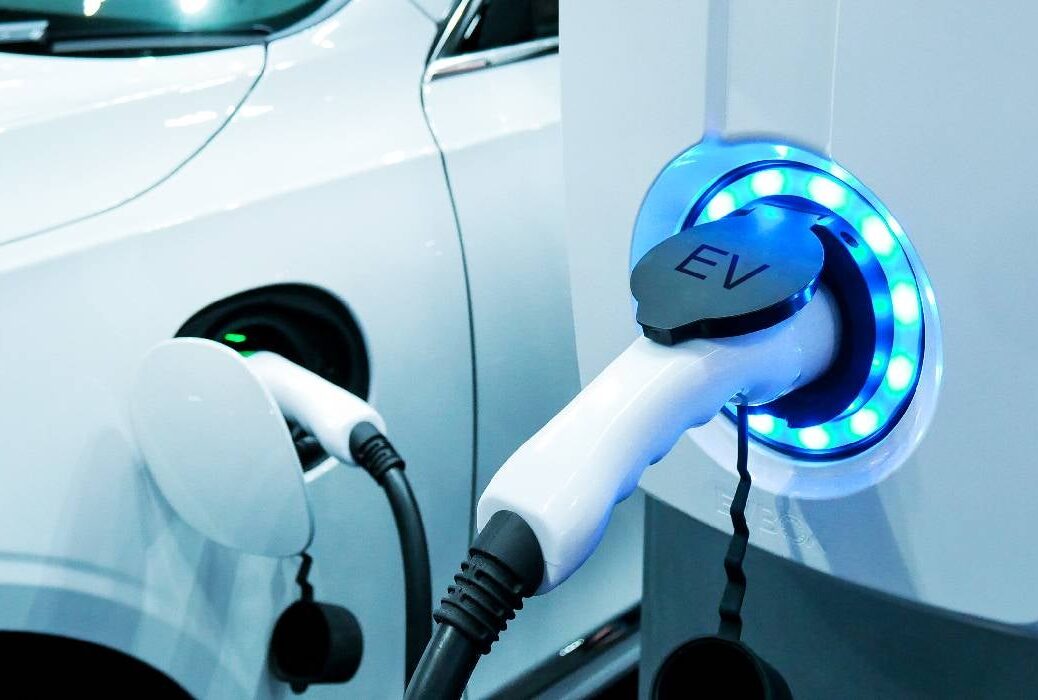
The appetite for electric cars is accelerating. In the five months to May 2021, battery electric vehicles (BEV) sales in the UK were up more than 145 per cent year-on-year, reaching a market share of 7.5 per cent. Globally, there are now more than ten million electric cars on the roads.
Britain’s policymakers are also enthusiastic. The government has announced a £1.3bn funding provision for a vehicle charging network, a centrepiece of its “Green Industrial Revolution”. Production, too, is speeding up. Carmakers including Nissan are planning “gigafactories” for the production of car batteries in the UK, while Jaguar pledges to go all-electric by 2025.
Johnson Matthey is one of the British technology companies supporting this activity. It is building a new plant in Poland that will be producing eLNO, its new-generation battery cathode material developed at its Oxford research base, within the next three years. Another plant is planned in Finland. eLNO should reduce battery costs, boosting range and consumer confidence. The plants, powered by renewable energy, will also help carmakers decarbonise their supply chains.
But while the electric revolution looks promising, it is only one part of a wider revolution that is needed to cut carbon emissions. The Intergovernmental Panel on Climate Change warns that “no single solution or option can enable a global transition to 1.5°C”. If the world is to achieve the G7 leaders’ pledge to halve emissions by 2030, more technologies will be needed, and fast.
Fuel cell future
Current battery technologies are improving but have limitations. This is particularly true for the competitive HGV market, where time spent charging and refuelling is lost revenue.
“Businesses need their long-haul commercial vehicles to have a long range between fuelling stops,” explains Johnson Matthey’s technical director, Andy Walker. “Very big batteries are required to provide this range, and such batteries are very expensive and heavy, so you’re penalising the operator up front. Bigger batteries also take longer to recharge.”
Ironically, the solution to this modern-day problem could be a 19th-century technology – fuel cells. Electrochemical fuel cells were first invented in 1839 by a Welsh judge, Sir William Grove. One hundred and thirty years later, fuel cell technology helped the first humans reach the moon. In both cases, Johnson Matthey supplied vital materials: platinum for Grove’s fuel cell; electrocatalysts for the fuel cells used by Apollo 11.
Fuel cells use hydrogen − the most abundant element in the universe − to generate power electrochemically. The only emission is water.
As well as being clean, a report produced by McKinsey for the Hydrogen Council claims that fuel cell buses, trains, trucks and even SUVs could be cost-competitive with diesel by the end of the decade.
Given this potential, Johnson Matthey has opened a new facility in China with the capacity to make enough membrane electrode assembly (MEA) components to power more than 10,000 hydrogen buses and commercial vehicles. It complements the company’s dedicated MEA manufacturing site in Swindon.
Companies are also pooling their resources. IMMORTAL − a Europewide scheme with a goal of developing high-performance fuel cell components − connects a consortium of academia and industry leaders, including Bosch and Johnson Matthey.
Nonetheless, despite the considerable advantages of hydrogen, it is still only an emerging technology. More research and investment is required − and the right conditions will be needed for it to take off. “Take the hydrogen refuelling infrastructure,” says Walker. “You need that in order to build a nascent industry. We’ve seen big battery technology investments like the Faraday Battery Challenge, which is really helping the advancement of battery technology in the UK. We’d like to see a Faraday for fuel cells to keep the UK at the forefront of fuel cell technology.”
Catalysing change
These limitations on both fuel cells and batteries mean that the almost 40 million vehicles currently on British roads − most still with internal combustion engines (ICEs) − must be part of any solution. Especially since the 2030 ban on new ICE vehicles will still allow used cars to be resold.
Catalytic converters will therefore continue to play a crucial role. These use precious metal catalysts – typically platinum and palladium − to convert harmful emissions from vehicle exhaust gases into carbon dioxide, water and nitrogen.
Vehicle manufacturers have also achieved significant reductions in average CO2 emissions by pairing advanced catalyst systems with hybrids and more efficient engines.
Today, one in three new cars on the planet uses Johnson Matthey’s catalytic converters, which prevent an estimated 20 million tonnes of pollutants being emitted annually.
One solution that’s proven valuable in polluted urban areas is retrofitting. A programme that started during the 2012 London Olympics has to date seen around 1,400 of the UK capital’s older buses fitted with emissions control catalysts and filters developed by Johnson Matthey and its partners. The benefits include reducing emissions of dangerous nitrogen oxides by up to 80 per cent. A further 2,150 buses around the UK have also had their emissions controls upgraded.
Catalytic converters are also part of a highly efficient process. “We sometimes say that we pioneered one of the world’s first circular economies,” says Walker. “The precious metals in emissions control catalysts are very expensive. So we recycle them, and get as much of that recycled material back into supply chains going forward.”
The right road
We still have a long way to travel on the road to zero emissions. A lower-carbon future relies on us pulling on all of the technologies available, and working together to bring new ones into play. “It’s not about the type of hydrogen we use,” says Walker. “It’s not about battery electric vehicles, or fuel cell electric vehicles. We’re going to need everything. Net zero is a tremendous challenge, and we’ve got to throw everything we can at it.”