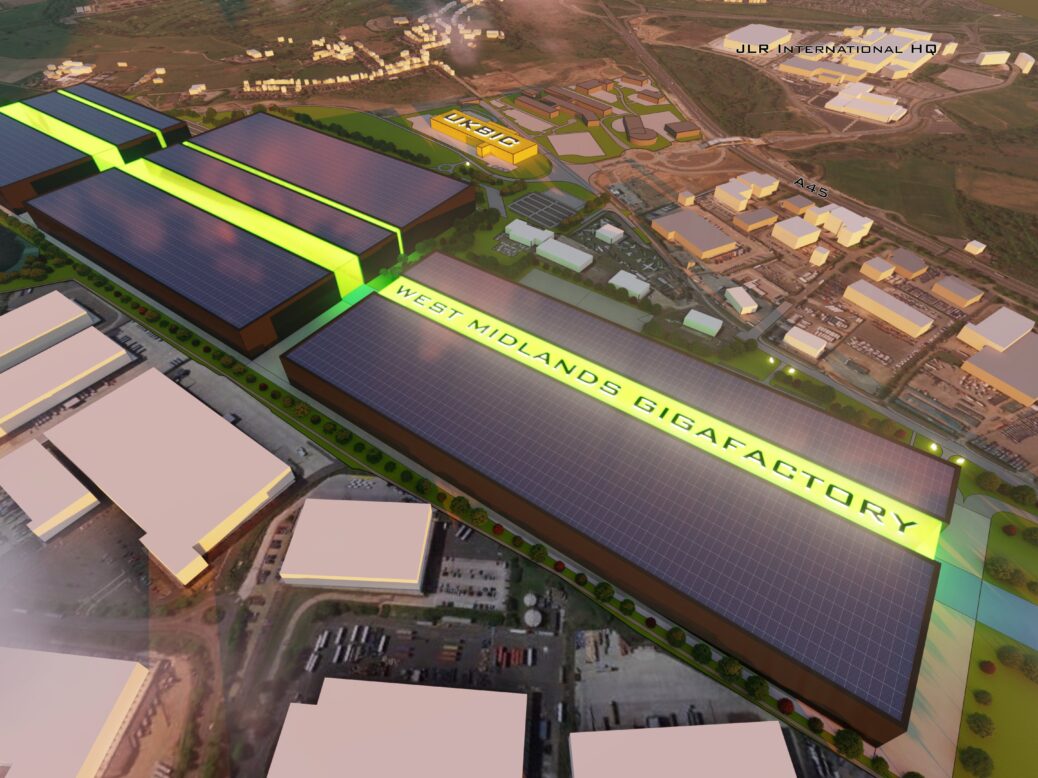
The future of automotive is electric. The government has, quite rightly, committed to phase out petrol and diesel vehicles in the UK by 2030. In fewer than ten years, all new cars sold will be electric.
This is the biggest change to our automotive sector since the internal combustion engine. It is a fundamental threat, but it is also an opportunity for this iconic British industry. In Coventry and Warwickshire, we are leading the way in electrification and delivering for UK PLC.
Within an electric vehicle, the battery makes up around 40 per cent of the value. They are also difficult and expensive to transport. As a result, future manufacturing and supply chains will be fundamentally reconfigured to bring car manufacturing closer to battery production.
This is the primary threat to the UK automotive sector. If we do not secure battery production in the UK, the automotive sector will gradually leak away to those countries that can meet its needs. This will not happen in one “big bang”, but will be a gradual effect that mirrors the decline of British manufacturing since the 1970s.
The answer lies in “gigafactories”. The term has been popularised by Elon Musk and Tesla but refers to any facility that manufactures batteries at scale. They are extremely specialised, and hugely expensive to deliver – with potential investments of around £2.5bn needed to become operational.
The Faraday Institution, a leading independent research institute, has estimated the UK will need between five and eight gigafactories to meet domestic demand. According to the organisation, if we do not secure battery production in the UK, we will miss out on 105,000 jobs by 2040. However, if we can secure a gigafactory, 78,000 new jobs will be created. There are currently no such facilities in the UK, and we are behind our international competitors in Europe, Asia and America.
The West Midlands is the beating heart of the UK automotive sector. The region employs around 46,500 people in automotive manufacturing, with an economic value of £3.2bn gross value added (GVA). Around one-third of cars come from West Midlands’ production lines, along with one-quarter of engines.
The region is home to 20 vehicle manufacturing sites and 35 automotive manufacturers, while more than 20 per cent of all UK automotive parts and accessories are manufactured there – the most of any UK region. More recently, the West Midlands has been rapidly building specialisms in future mobility technology. It is the UK’s first Future Mobility Zone. Connected and autonomous vehicle trials have taken place in the region, including the UK’s first self-driving vehicles taking to roads in Coventry city centre.
The result is a powerful automotive cluster and skills ecosystem that is ready and willing to be reskilled and upskilled to take advantage of electric vehicle technology. If the West Midlands is the home of UK automotive, Coventry and Warwickshire is a centre of excellence in battery technology, research and development. This is a result of years of hard work from Coventry City Council and the local partnerships.
The Advanced Propulsion Centre (APC) is located at the University of Warwick and is a joint venture between the UK government and the automotive industry. Warwick Manufacturing Group is a partnership between the University of Warwick, Jaguar Land Rover and Tata Motors.
Jaguar Land Rover’s global headquarters are in Coventry and Warwickshire, along with others including Aston Martin Lagonda, London EV Company and Lotus Engineering. Critically, Coventry is home to the UK Battery Industrialisation Centre (UKBIC), which is the centre of battery research and development in the UK. The facility is being delivered by a consortium made up of Coventry City Council, Coventry & Warwickshire Local Enterprise Partnership (LEP), and WMG, an academic department at the University of Warwick. The purpose of UKBIC is to scale up and commercialise technology central to the manufacture of batteries, thus supporting the development of gigafactories in the UK.
The consortium secured government funding in 2017 through the Faraday Challenge, and its delivery has reinforced Coventry and Warwickshire as the heart of the UK’s response to battery research. UKBIC proves that Coventry and Warwickshire can deliver for UK PLC. Coventry Airport has been identified as the preferred site for a West Midlands gigafactory, backed by Coventry City Council, Coventry and Warwickshire LEP, West Midlands Combined Authority, Warwick District Council, and Warwickshire County Council – as well as the private sector.
A gigafactory at Coventry Airport would create at least 4,500 jobs directly as well as protecting and creating tens of thousands more in the supply chain. The airport’s location – a stone’s throw from UKBIC, and at the heart of an advanced automotive ecosystem – makes it an ideal location for up to 5.7 million square feet of manufacturing space. Coventry City Council has seized the initiative by forming a joint venture partnership with Coventry Airport to secure planning permission for a gigafactory. This is being funded at risk by both parties because we understand how critical this is for our economy and future job creation. We have made huge progress in understanding what is needed to secure a gigafactory and early discussions are already under way with potential manufacturers and customers.
Local government is playing its part, alongside the private sector. We now need ministers to back our vision. The government has made £500m available to secure battery manufacturing in the UK. The time is right to work with us to develop an attractive package of support to secure investment in a gigafactory at Coventry Airport.
We have the site, we have the skills, we have the experience, and we have the innovation. We are the obvious location for the first UK gigafactory and will work with the government to make it happen
Jim O’Boyle is cabinet member for jobs, regeneration and climate change at Coventry City Council