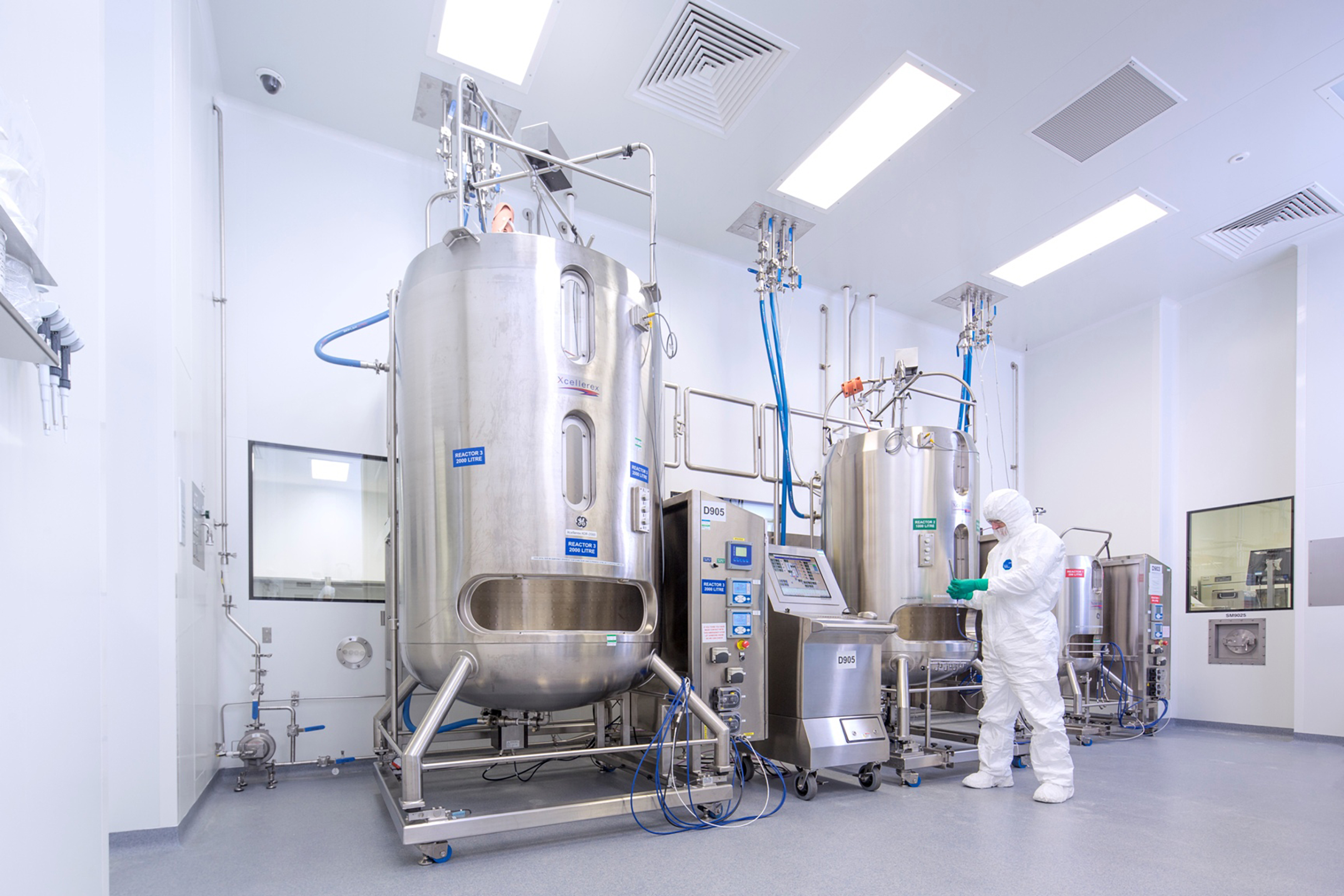
FUJIFILM Diosynth Biotechnologies (FDB) is a contract development and manufacturing organisation (CDMO). It offers complete solutions to the biopharmaceutical industry – from preclinical investigations and process development to commercial current good manufacturing practice (GMP) production, fill-finish and final product packaging. It brings its expertise to support companies that are developing therapies and vaccines all the way through the drug development journey.
Can you walk us through the basics of biotechnology?
MM: Biopharmaceutical manufacturing uses living cells to produce molecules that are too large and too complex to synthesize chemically. This manufacturing is enabled by recombinant DNA technology. This means that genes are engineered into different systems for expression in host cells. There is a wide range of modalities, which include cell culture, microbial fermentation and viral vectors, to mention the most commonly seen in our industry.
How do you work with other organisations?
MM: As a CDMO, we collaborate with our customers to support them as they advance their medicines through the drug-development process. It is very important to note that our customer owns the process and the product. We can support from the very early stages all the way to providing commercial supply once the products have been approved by the regulatory agencies. As a CDMO we work with a variety of customers, some developing vaccines, some gene therapies, others therapeutics, to name a few. Because of this diversity, drug developers have a variety of requirements. This creates an ever-changing development and manufacturing portfolio that we manage as an organisation.
How do companies select a CDMO?
MM: Customers demand quality, speed and flexibility. Their selection criteria usually involve reviewing a CDMO’s technical expertise to develop processes that can be scaled up as demand increases. Customers also consider manufacturing capabilities and available capacity. This is important as customers are driven by timelines. Having a strong compliance track record is an essential part of the selection process. Our quality systems are constantly evaluated through due diligence, customer and regulatory agency audits.
What does it take to make a biologic therapeutic or a vaccine available to patients?
MM: The drug development process can range from ten to 15 years, not including the discovery and very early development stages. This is driven by the need to have stages during human clinical trials, which are typically phase one to phase three. As the product meets clinical trial endpoints, it moves to the next phase. As it moves the number of patients dosed usually increases, all depending on the indication, patient population, frequency of dosing, among many other factors.
As a CDMO, having the ability to scale up processes consistently while meeting the critical quality attributes of the product is essential. One point to make about this process is the current race to deliver a Covid-19 vaccine and other therapeutics to treat
Covid-19-related ailments. The challenge that we now face as an industry is that we need to do what takes years at an expedited rate. We have a desperate need to deliver vaccines that will stop the spread of the Covid-19 virus and therapies to halt the mechanism of action inside the body once a person is infected.
What is the role of a CDMO such as FUJIFILM Diosynth Biotechnology during this crisis?
MM: The current pandemic is a complex and challenging situation that has brought together a wide array of parties from private industry, governments, regulatory agencies, academic institutions, suppliers and transportation, to name but a few. There is, of course, the identification of potential vaccines and therapeutic agents and moving them quickly from a research setting into human trials. As this is happening, there is the question of the supply chain to support the efforts of all these groups.
How are they going to deliver the needed doses, whether it is a vaccine or a treatment, globally?
Having the ability to move things swiftly into GMP production is extremely important. As a CDMO we are playing a role in this space as we have operational capabilities that can (and are) being quickly ramped up. We have a global footprint with facilities in the United States and Europe that can accommodate the different modalities explored today for Covid-19.
What are other challenges that you see in your industry at this time of Covid-19?
MM: The challenge we have today is to prepare for the future. In order to do this we all need to think of the questions that we need answered in order to provide a solution. We need to strive for balance. There is a need for lean capacity all over the world, there is a need for a supply chain that will allow for these products to be stored (think future stockpiles) and delivered all over the world. The pandemic has created a global level conversation that we must continue.