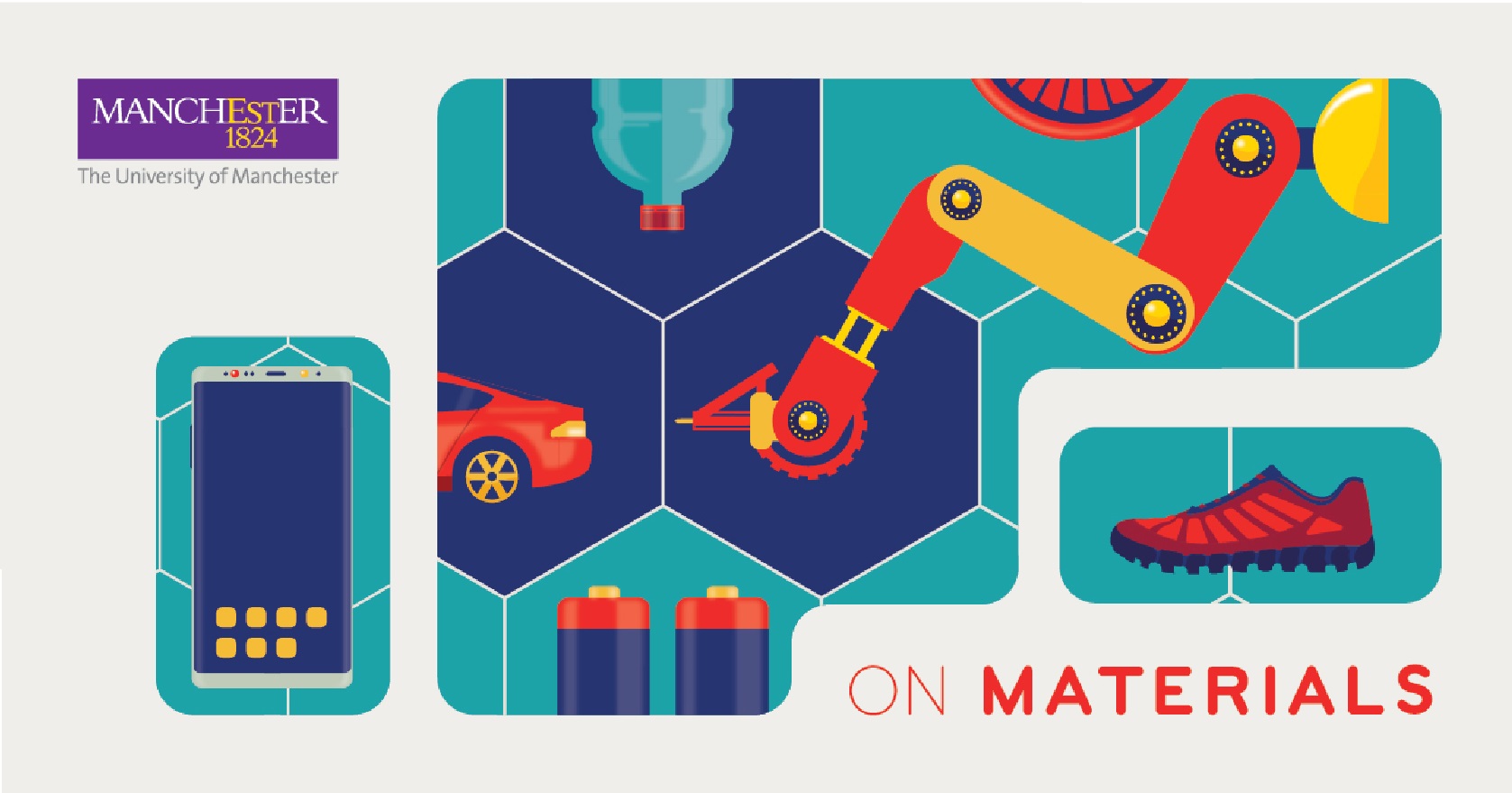
Graphene is 15 years old but is already recognised as a teenage superstar. This single layer material, originally isolated at The University of Manchester in 2004, has inspired not only great science but potentially disruptive innovation.
Graphene has been adopted into a range of manufactured products. One of the most recent has been the BAC Mono R supercar. This iconic British marque is made by Liverpool-based Briggs Automotive Company Ltd and is the world’s first production car to fully incorporate graphene-enhanced carbon fibre into every body panel. In this case, the reason is to make the car faster but there are also potential productivity benefits in terms of reduced material and manufacturing time.
Another step forward has been taken by inov-8, the specialist British-based sports shoe brand, who have worked with graphene scientists at Manchester to develop rubber outsoles that deliver the world’s toughest grip. They have successfully launched the G-Series range of footwear that has taken the market by storm.
These examples point to a tipping point in the widespread adoption of graphene and related materials across the manufacturing base.
And it all began when graphene was isolated at The University of Manchester by professors Sir Andre Geim and Sir Kostya Novoselov who, in 2010, were awarded Nobel Prizes. Their success has been galvanising and researchers worldwide have followed the trail blazed by Manchester and have criss-crossed the Periodic Table on intrepid quests to find other similar nanomaterials. And they have succeeded to the point where we now have distinct categories of 2D materials, such as a group of single-element graphene analogs called Xenes or a large set of metal carbides dubbed MXenes (pronounced ‘Maxines’).
These many graphene-inspired 2D materials – which I call the ‘Graphenes’ family as a helpful shorthand – are all very exciting in their own right, each offering distinct advantages in terms of say conductivity, filtration, thermal management, lightweighting or sensor capabilities. But far more importantly is the way we can use various types of 2D materials as building blocks to create ‘designer materials’ with truly novel features on demand.
According to my Manchester colleague Regius Professor Phil Withers from the Henry Royce Institute, the materials industry in the last century had been driven by ‘drop-in’ substitution as new materials, such as synthetic polymers and plastics have resulted in the formation of important materials-based industries. But the focus has since moved from simple substitution to the creation of customised materials having tailored functionality, from super-smart composites with inbuilt sensor and visualisation technology to magnetic materials for data storage.
These customised materials, I believe, will be based on the Graphenes family and their impact will be seminal. Historically game-changing materials have defined their time (such as the Iron Age, the Stone Age, the Bronze Age, the Steam Age, and more recently the Silicon Age or Computer Age) and I suspect the ‘Graphenes Age’ is now fast approaching.
The tailored functionality of this new generation of Graphenes-based materials will significantly impact on advanced manufacturing and how we manage the value chain, including design and engineering; materials supply; equipment and tool-making; additive and automated manufacturing systems; testing and support services.
I recommend that the UK’s innovation sector acts to prepare the manufacturing base for a huge transformation in its processes and methods of manufacture – and to be Graphenes-ready. It will be a new generation of advanced materials that is likely to produce a real paradigm shift on manufacturing rather than the current factors being focused on today around digitalisation.