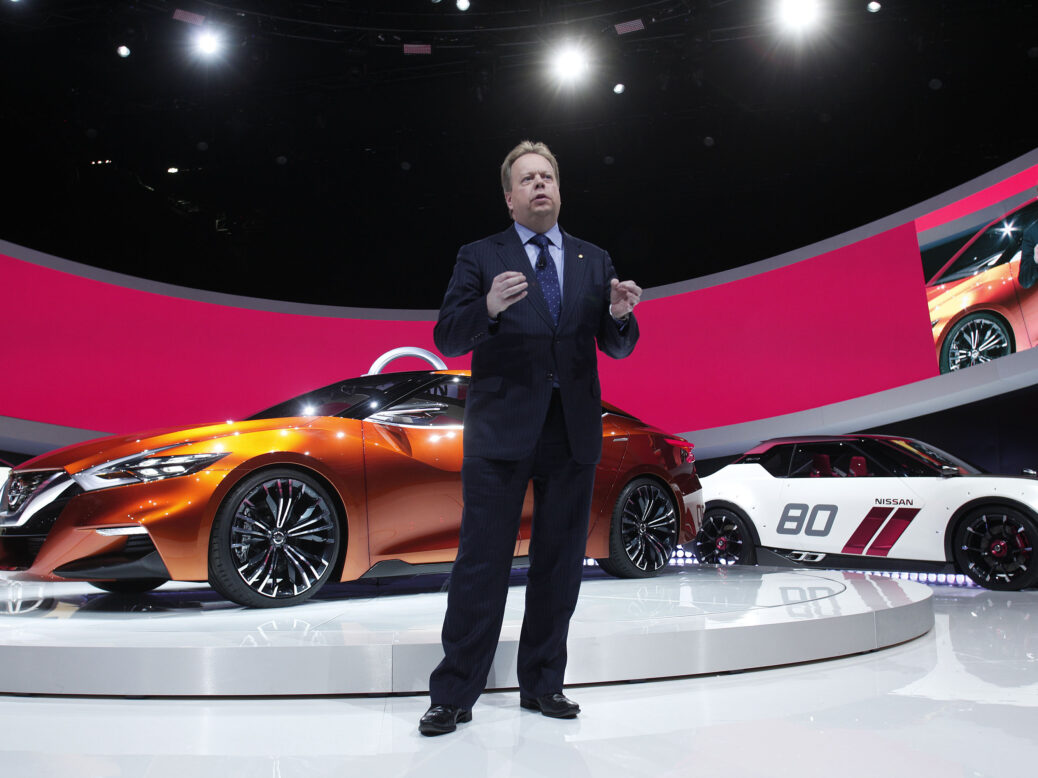
Editor’s note: This article was originally published on 3 February. On 27 February Recharge Industries bought Britishvolt out of administration. This interview is being repromoted in light of the news.
It was all looking so promising: a multi-million pound valuation, the promise of a massive home-grown factory for cutting-edge automotive technology, and a name that sounded reassuringly patriotic. Then it all came crashing down. Last month Britishvolt, the company that had promised to save Britain’s car manufacturers by building a gigafactory for battery manufacturing in Blyth, Northumberland, called in the administrators.
By the time EY was called in at the end of January Britishvolt had raised £200m from investors including the mining giant Glencore, but it had no viable product and a paper-thin order-book. It owed an estimated £120m to creditors and there have been reports of decadent behaviour by management, who are said to have travelled by private jet and supplied staff with electric Porsches (though the company’s management has said that such reports were overblown).
On the sidelines of this drama stood Andy Palmer, the former chief executive officer of Aston Martin and chief operating officer of Nissan, who is known as the “godfather of the EV” for his role in the development of the Nissan Leaf, the world’s first mass-market electric vehicle. Having left his job at Aston Martin in May 2020, Palmer spent the next couple of years taking on roles that focused squarely on EVs: as chief executive of Switch Mobility, the electric bus and van start-up, and as chairman of the Slovakian battery maker Inobat.
For years Palmer had been warning that the UK’s future as a power in automotive manufacturing – 800,000 jobs are thought to be dependent on the sector – was at risk unless it began to take battery manufacturing seriously. Now he was watching one of the few hopes crumble. The fall of Britishvolt was “an indication of almost my worst nightmare”, he tells Spotlight. But it was also, probably, inevitable. The product Britishvolt was developing, he says, “wasn’t something that was exemplary”. “If you’re a startup you’ve got to offer something different, or more than, the main players,” Palmer adds.
Reports have indicated that Inobat may be planning to buy the Blyth site, a massive former coal-fired power station that Britishvolt had spent £70m on groundworks for. Palmer won’t comment on whether Inobat is still in the mix, although he will say that it hasn’t decided where to situate its first factory. The choice is between the UK (it had originally been looking at a site in Teesside) and Spain, where in October the company signed a declaration of intent with the government to fund a €3bn gigafactory. The company will make a decision sometime in the second quarter of this year, says Palmer.
The decision is proving tough, though. The UK has “a decent law system, the English language, you’ve got a well-trained workforce”, says Palmer. Spain offers other incentives: whereas Britishvolt had been promised a £100m investment from the British government, the incentives offered by EU countries are “two or three times as much”.
This is the crux of the issue, says Palmer, and the reason the UK’s car industry will suffer. “The countries that are winning today are those where the governments are most interventionist,” he says. Take China, which 15 years ago identified electric vehicles as a priority. In the intervening period its government has “had a philosophy of acquiring intellectual property around EVs, and as a result of that 65 per cent of EV batteries are made in China”. The EU’s reaction to that was to draw up a regulatory framework demanding that batteries were 65 per cent made in the EU. Meanwhile the US’s inflation reduction act is offering big incentives in the form of tax credits to battery makers to move to the US.
“The [UK’s] political ethos assumes that there should be a small state and no state intervention in the auto market,” says Palmer. “The problem is that we we’re in a global market where the level the playing field isn’t level. In other words, other governments interfere.”
There are other problems with the UK. For a start, there is little industrial strategy (the government now has a “Plan for Growth” and related strategies), which Palmer says leaves the government open to accusations of being reactive, rather than proactive. “There is an overwhelming tendency for political figures and parties to look for immediate satisfaction on social media rather than following a long-term, well thought-out industrial strategy,” he says.
For another, there is simply a lack of enthusiasm, which is putting battery manufacturers off coming to the UK. “A battery is typically 400 to 500 kilograms, and typically the size of the platform of your car,” says Palmer. “It is big, heavy and expensive, so what you don’t want is long supply chains. Ultimately, it’s cheaper to put your car factory near to where the battery factories are rather than the other way around.
“The battery factories will get built in Europe or China or Japan or the United States and therefore ultimately, the car factories will move closer to the United States because it’s easier and cheaper to move a complete car to the UK than it is to move a battery to the UK.”
Without gigafactories, he says, the UK’s car industry is “staring into the abyss”. There’s still time for the government to turn this around, though. First, it needs a convincing industrial strategy. Second, it needs a battery strategy. “Our battery strategy has got to support our industry but also the energy storage industry and the aviation industry,” he says.
The government must also be realistic about how this strategy – or an absence thereof – will affect industries outside of car manufacturing. The UK currently has one small-scale gigafactory up and running in Sunderland, which supplies Nissan with batteries for its Leafs; another is due to be completed by the middle of this decade. Estimates by Parliament’s Environmental Audit Committee, however, suggest the UK will need five more by 2027. Britishvolt’s collapse may have dashed those hopes.
“Government officials [keep] saying that we need a 90 gigawatt [manufacturing] capability in the UK by 2030, but that 90 gigawatts is cars only,” says Palmer. “It doesn’t include commercial vehicles, it doesn’t include aerospace, and most importantly, it doesn’t include either export or energy storage.” That means the UK’s requirements are much higher than estimated. “You’ve got to get out of these silos when looking at how you fund batteries: batteries are the new oil, you’ve got to fund it in that way.”
Ultimately, says Palmer, whether or not the UK continues to have a car manufacturing industry is the government’s choice. “It may decide that auto is not where it wants to be, but it’s then got to decide what to do with those 800,000 displaced jobs,” he says. And he is blunt about the risks: “If you don’t have battery manufacturing in this country, then ten years from now you won’t have an auto industry.”
[See also: Are we there yet with electric cars? The EV story – with Wejo]