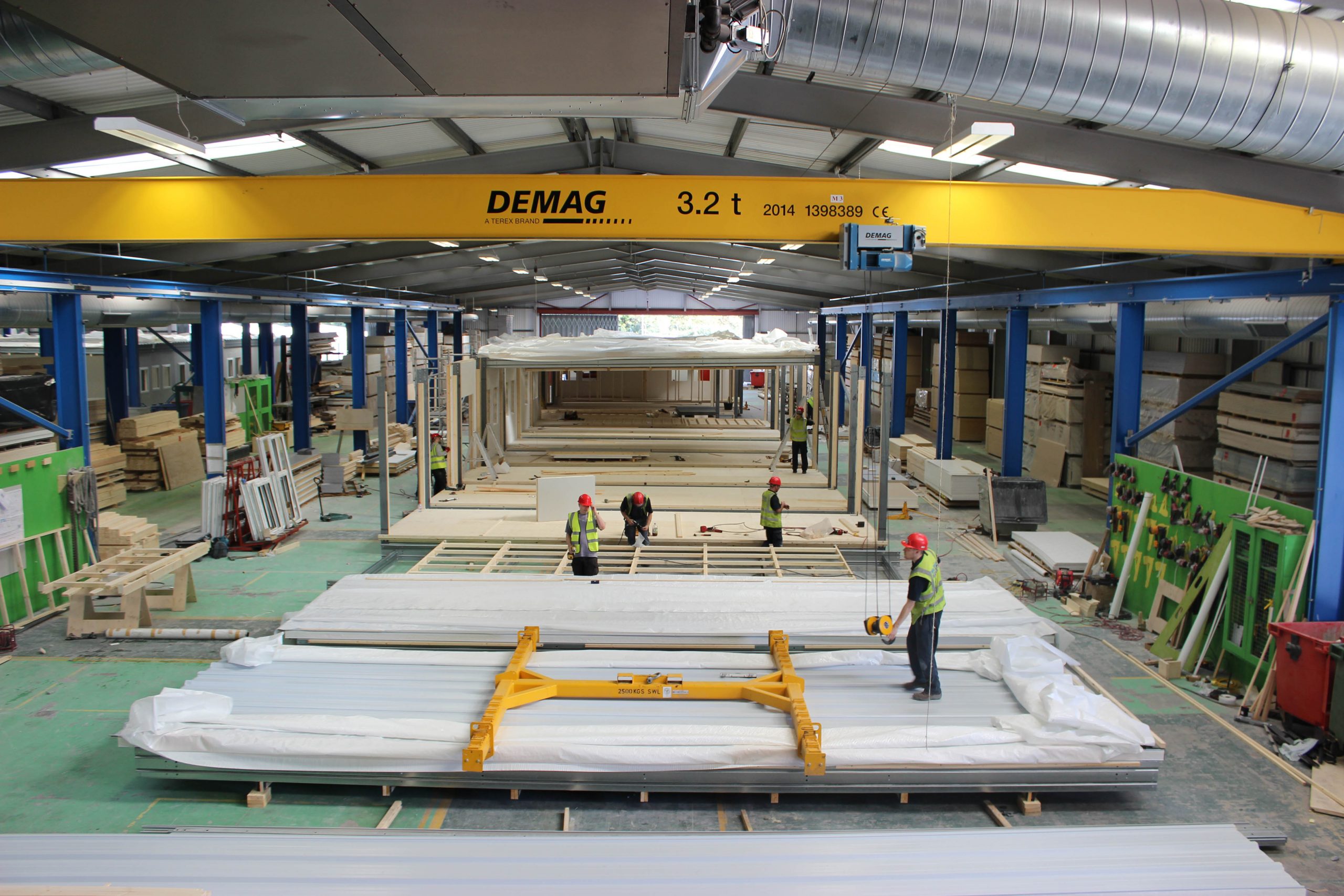
Modular construction (otherwise known as offsite or volumetric construction) is known for its speed. Manufacturing a building in a factory setting, while building work takes place onsite, reduces construction programmes by around 60 per cent. Compare this to the “traditional” route where the time taken to complete a building has changed very little in the last 30 years.
This speed, as well as the cost savings resulting from it, is why the UK government consistently supports offsite construction. But while speed is a major advantage, modular’s eco credentials are often overlooked.
Research by Swansea University’s SPECIFIC Innovation and Knowledge Centre led them to a modular solution for their pioneering “Active Office”. Their innovative building design combines readily available technologies to generate and store heat and electricity in one integrated renewable energy system. The building, which was funded by Innovate UK with support from the European Regional Development Fund through the Welsh Government, also supplies electricity to the local network and electric cars.
Working with Wernick Buildings, a modular specialist with 85 years in the industry, SPECIFIC ensured sustainability was at the heart of the building’s construction. “The desire to reduce the energy consumption of the building before considering energy generating technologies was fundamental to the project,” commented Joanna Clarke, architect and head of design.
It was this dedication that impressed Education Buildings Wales judges who awarded it the “Delivering a Sustainable Education Facility” prize at this year’s awards event.
The project is particularly important when you consider that 10 per cent of the UK’s carbon emissions are derived from construction. Unsustainable materials, waste which ends up in landfill, transportation of materials and labour and onsite generators are the largest areas of concern. However, inherent in the modular industry are substantial carbon savings.
Materials are locally sourced where possible and modules are built with standard material dimensions in mind, ensuring there is little waste.
Manufacturing buildings on a production line means that materials are delivered in bulk and excess materials are simply passed down the line to the next module.
Onsite, less operatives are needed as 90 per cent of the build is in the factory. That means fewer cars and deliveries. Disruption to the site’s surroundings is also minimised.
Carbon savings don’t simply end once the building has been handed over. Modular buildings are literally wrapped in insulation, making them far easier and much cheaper to heat. With the addition of solar technology, modular buildings can easily achieve carbon neutral and even carbon negative status, as demonstrated at Swansea University.
Stuart Wilkie, managing director at Wernick Buildings remarked: “We are committed to lowering carbon emissions for our clients. Modular buildings are the buildings of the future, and they’re here today.”
Reducing the impact of construction means big changes in the industry and a shift in the perception of modular buildings in society. Modular is ready to take over as the number one building method and we don’t have a minute to waste.