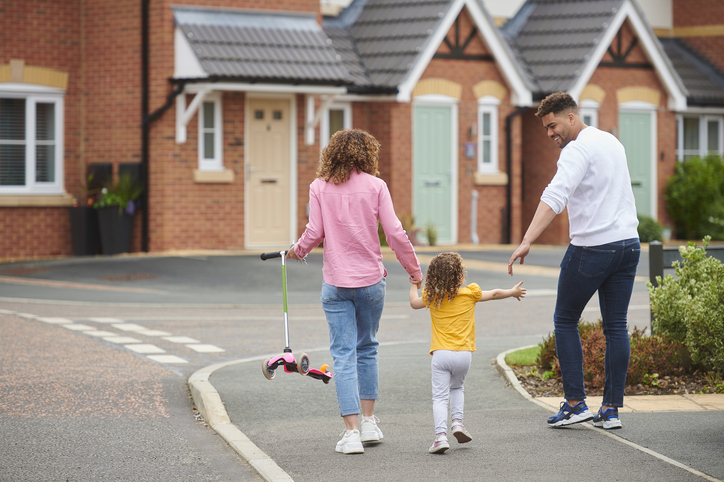
The government has put housing at the heart of unlocking growth in the UK, committing to deliver the biggest housebuilding programme in two generations.
The deliverability of building 1.5 million homes, the overhaul of the UK’s planning system and the impact on the green belt have so far dominated the debate. What receives considerably less airtime is quality: but we must consider how building at speed can create a new generation of properties that deliver the homes people want and which embed sustainability and safety. In the transition to net zero, properties must be energy efficient to reduce carbon and ensure lower bills for homeowners and renters. As the climate continues to change, homes must be built to be more resilient to increased rainfall and the growing threat of overheating.
As the construction industry learns the lessons of the tragedy of Grenfell Tower, a new generation of homes must, above all, be safe and fire-resistant. In 2025, the Future Homes Standard will focus industry on energy efficiency and carbon reduction in new home builds. However, embedding quality and safety into the fabric of our new housing stock must be a constant focus for housebuilders, registered providers, and local authorities. Concrete masonry construction has been central to how we build homes in the UK for generations.
Known as “brick and block” it is a tried and tested building technique representing 73 per cent of the new-build housing market. These materials have a proven safety record and do not burn, compared to combustible building materials such as timber which add additional risk to our built environment. Concrete does not require any additional fire protection because of its own built-in resistance to fire. With a clear roadmap to beyond net zero, the UK concrete and cement industry is continuing to evolve and innovate.
Masonry concrete is UK-made with local and responsibly sourced supply chains. As well as providing much-needed new homes, a new wave of housebuilding must prioritise and maximise the use of domestic materials. A reliance on imported, combustible materials with high “carbon miles” and vulnerability to disruption and delays from lengthy global supply chains will also undermine our ability to hit new completion targets. Materials are critical to delivering the government’s vision for new homes at volume but are often overlooked. Yet they are integral to meeting the quality, deliverability, safety and sustainability challenge. Now is the time to focus on tried and tested, domestically produced, long-lasting building methods to deliver future-proofed UK homes. Relying on imported combustible materials which add risk to our built environment and do nothing for UK manufacturing jobs is not the answer.
This article first appeared in our Spotlight Housing supplement, published on 29 November 2024.