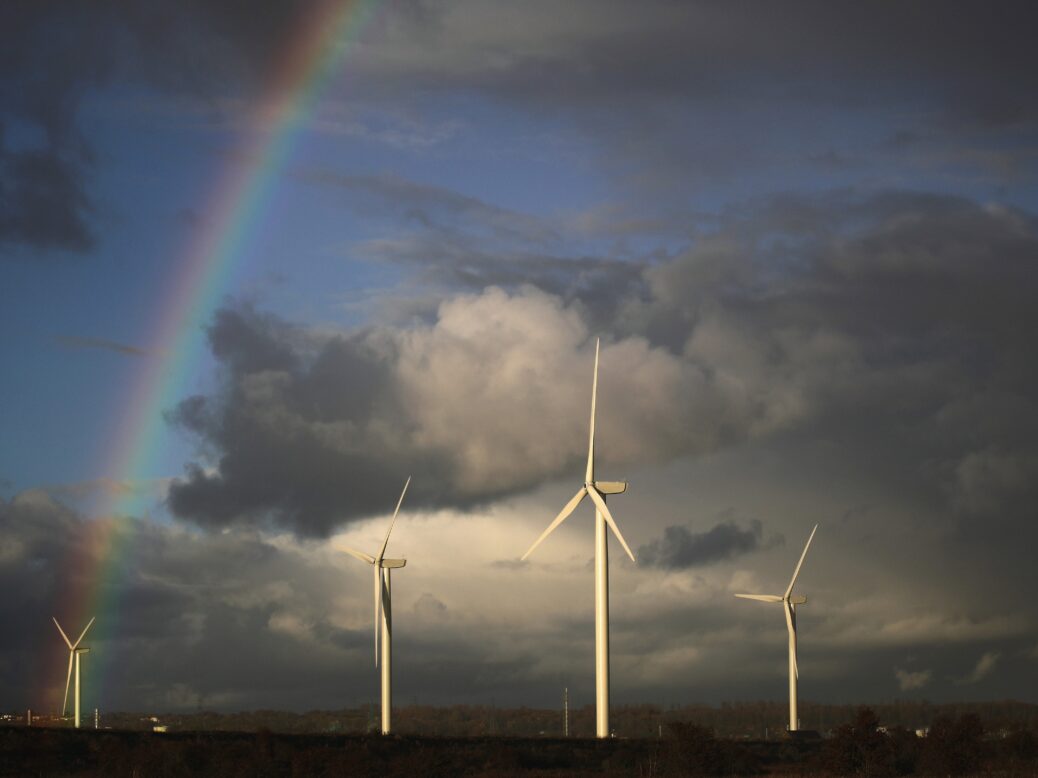
The journey to net zero is already well under way. Consider the countries that have, or are in the process of, committing to net zero by 2050; this is where just under half of the world’s gross domestic product (GDP) is generated. But the downside to that scale of economic production is waste: from agriculture, food and municipalities, and in the form of carbon dioxide. A lot of this waste is generated as a result of manufacturing processes being too “linear”. And removing this waste without using landfill or incineration is a huge issue. Without taking a new approach to waste – and moving away from a linear processing approach – hitting net zero will be impossible.
One solution is “circularity”: recycling and re-using waste streams and products to create a closed-loop system, which minimises resources and the creation of waste, pollution and carbon emissions. As we journey towards net zero, these “circularity” principles are increasingly embedded in the research and design of products.
As a leader in sustainable technologies, Johnson Matthey is striving to help the chemical industry transition. Martin Hayes, biotechnology lead, explains: “More and more companies are starting to move away from linear chemical processes to circular ones – which is definitely a step in the right direction – by looking at how the waste from chemical processes may be the source for biological processes. For example, biological entities, such as enzymes or organisms, can be used to recover precious metals from waste streams, maximising value while reducing waste.”
Another example is the use of gas fermentation to upgrade waste products, particularly carbon dioxide and hydrogen, and convert them into chemicals. Hayes adds: “In this instance, by linking biology and chemistry to get the desired end product without affecting the customer experience, but making the process much cleaner.”
As a large contributor to greenhouse gas emissions (GHGs), food waste is another issue. But a circular approach can help here as well. Food waste can be fermented to convert it into something more useful, such as renewable chemicals. “What is valuable about this is that it means that these chemicals are not produced from virgin fossil material,” says Hayes.
However, in order to use these technologies efficiently, we need to be clever about how we collect waste streams – for instance, by collecting process waste streams at centralised or distributed sources so that they can be used as fermenter feedstocks. And to realise the potential in these technologies and new businesses, it’s important to take a collaborative approach and for multidisciplinary teams to work together. Hayes continues: “We know that getting the biology to the end product requires engineers, chemists, microbiologists, biochemists, different scientists working together with commercial expertise to make a product that is sustainable, has a low environmental footprint and is still profitable. We work collaboratively in partnership because we recognise we need to develop these solutions in ways that reflect the needs of each client and the broader society.”
But the scale of the issue shouldn’t be underestimated. Scaling up and optimising processes such as fermentation can be resource-intensive and involve large volumes. That type of process intensification needs engineers and chemical engineers to make it smaller and more efficient.
While the UK leads in renewable technologies, it is also important to think in terms of connected systems rather than isolated applications of technology. That broader perspective in a circular system will get us towards net zero.
Regulation can arguably play a role here, to incentivise the use of sustainable alternatives over conventionally produced fuels and chemicals. This may include the introduction of greater penalties for the generation of waste or supports that encourage re-using and upgrading the waste products. Ultimately, the regulatory environment could help to accelerate the transition to net zero.
One way governments can help is by reforming the legislation on the production of chemicals to level the field in favour of more sustainable alternatives to petrol and oil. But incentives will be needed to encourage companies to make this shift. Employing a carrot-and-stick approach could see greater penalties for waste, like a carbon tax, that encourage re-using and upgrading the waste products. If this works well the situation will be reversed and organisations will be paid for their waste – it will completely revolutionise the way we approach waste.
But before legislation is introduced to incentivise a move to the sustainable practices that are needed, there is an opportunity for industry to embrace these technologies and systems now. Hayes concludes: “It requires technologies to make this happen and that is where Johnson Matthey can help. Businesses that are not prepared for that move will find it costly, whereas those who are already on the journey to net zero and the circular economy will reap the benefits.”