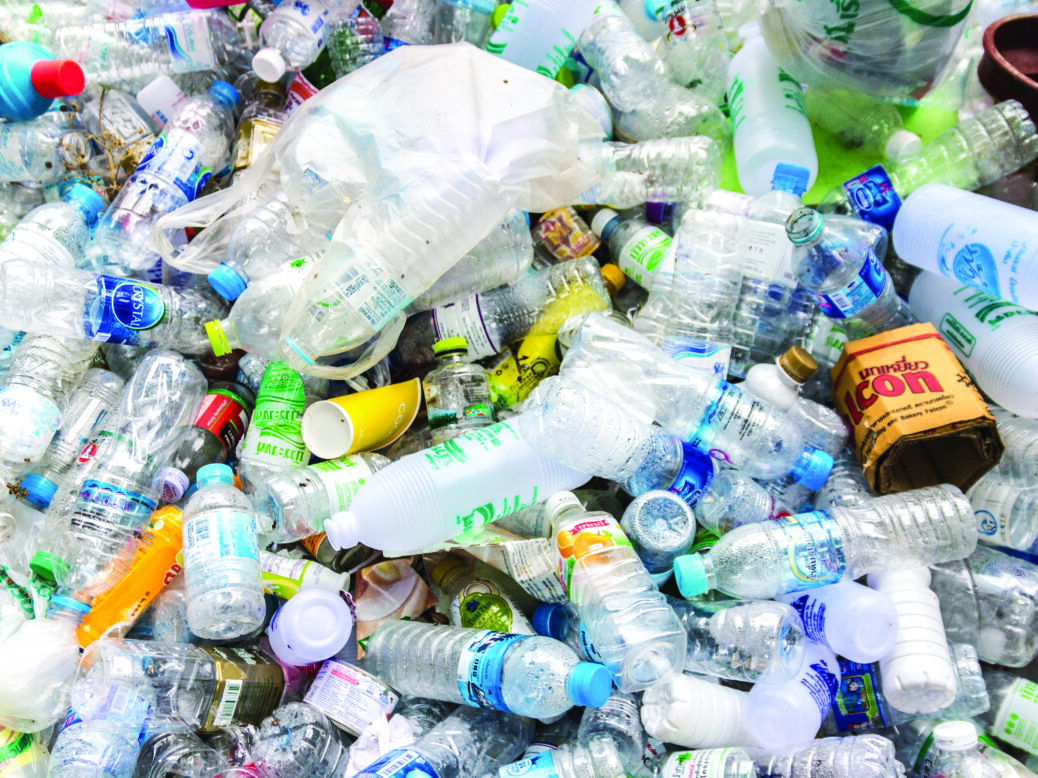
In the 1985 sci-fi film Back to the Future, Emmett “Doc” Brown drives a time-traveling, flying DeLorean that uses garbage for fuel. And although the majority of that scene will likely remain confined to Hollywood, in 2018, given the sheer amount of it, the idea of using plastic waste to generate power is perhaps not a bad one.
Plastic is the collective term given to a large family of synthetic materials derived from organic polymers, such as oil, coal or natural gas, that are able to be moulded into different shapes, usually by being exposed to extreme heat and pressure. As plastics are strong yet flexible and cheap to produce, they make effective cases and containers. Plastics have established themselves as a mainstay of the modern human experience, but their widespread use – in food packaging and electronic equipment, for example – has paved the way for the problem of plastic pollution.
A study published by the academic journal Science Advances found that of the roughly 8.3bn metric tonnes of plastic that had been produced since the material’s introduction into the manufacturing mainstream in the 1950s up to 2015, 6.3bn had become plastic waste. Nearly 80 per cent of all plastic, the report added, winds up as debris in landfills or in the world’s oceans.
The Spanish chemical recycling company Plastic Energy, which has plants in Seville and Almeria, as well as a newly opened technology HQ in London, is trying to address the problem of plastic pollution while creating a renewable energy resource that can do something good with the vast supply of plastic waste that humans continue to produce.
The company, its head of PR Richard Peel says, receives “raw end-of-life plastic waste from sorting facilities and recycling factories [in Spain]” before applying a patented “thermal anaerobic technology [TAC] process” to turn the “rubbish that would otherwise end up being incinerated, in a landfill or in the sea, into an oil that we call TACOIL”.
Via the TAC process, Peel explains, plastics are “heated in an oxygen-free environment”, where the vapour is then distillated to form TACOIL, which can be used to “produce new plastics or as an alternative fuel source” following condensation and refining.
How effective is TACOIL as a fuel source? Plastic Energy has already achieved proof of concept, in part, Peel says, by supplying some of the fuel used in the On Wings of Waste research project, which involved the British pilot and environmentalist Jeremy Rowsell flying a light aircraft across Australia in 2017. Rowsell flew a Vans RV9a plane the 500 miles from Sydney to Melbourne, using a blend of fuel of which ten per cent was made up of TACOIL. While at first glance this might appear to be a “modest figure”, Peel says that if scaled up this could have a “significant effect on the aviation industry”.
Consider, for context, that a typical Boeing 747 plane on a 10,000-mile flight burns through about 36,000 gallons of fuel and, according to the International Air Transportation Association, a fifth of most airlines’ operational costs are spent on fuel supply. Were ten per cent (3,600 gallons) of plane fuel to be sourced from TACOIL, that would equate to about 16 tonnes of plastic waste, in theory at least, being saved from landfills or the ocean on every 10,000-mile flight.
Could TACOIL eventually represent more than ten per cent of a fuel blend? Could it replace fuel entirely? Peel says: “I’m confident that this has the potential for upscale, yes. But in the early days, as with any innovation, there will always be some initial scepticism. We had to use ten per cent [for On Wings of Waste], because at the end of the day, we were sending a human being up in a plane and it’s someone’s life we were talking about. Thankfully, it worked, but it’s best to start small and then scale up. In the future, yes, I think we could be seeing more TACOIL-led fuel solutions but just as important is our ability to turn waste plastic back into plastic.”
Currently, Peel says, Plastic Energy has “arrangements with Spanish recycling and waste management companies” to supply it with plastic waste, with the firm’s biggest market being “mainly fuel for transport in Spain”. More than six million litres of TACOIL output has been produced to date. He adds that Plastic Energy’s long-term aim, towards which the London technology HQ is a “giant step”, is to “expand the product globally”. Peel envisages a plant in the United Kingdom “hopefully sometime very soon”.
Will the UK’s decision to leave the European Union affect this ambition? “Of course Brexit will be a consideration,” he says, “but I’d hope that an innovation like this would be something that attracts investment, independent of politics.”
At Swansea University, a team of scientists led by Dr Moritz Kuehnel is working on a chemical process to convert plastic waste into hydrogen. The process, “photoreforming”, involves adding a light-absorbing material to plastic waste before placing it in an alkaline solution, which is then exposed to solar energy. “We have developed a special coating made from cadmium sulfide,” Kuehnel explains, “that makes the [plastic] very robust and highly active for photoreforming when placed into alkaline water, which is water containing sodium hydroxide.”
The Plastic waste, Kuehnel says, is cut up into more manageable-size strips. The “photocatalyst” is then applied before sunlight or a simulator lamp is shone onto the solution. “Upon irradiation with sunlight, the quantum dots form a charge-separated state characterised by excited electrons and holes, similar to a solar cell, where excited electrons and holes are used to generate electricity. The excited electrons convert water to hydrogen. The hydrogen gas forms as bubbles and evolves from the solution.”
As traditional mechanical recycling plants use “expensive and time-consuming” cleaning and sorting processes to separate plastic waste by quality and type, Kuehnel claims that chemical methods of recycling can avoid this issue altogether. He points out that the residue of whatever a plastic container used to hold, “for example grease or oil”, can cause complications for recycling.
“The sorting and cleaning of plastics is very costly, and the actual recycling process requires energy, namely heating. In contrast, photoreforming only uses sunlight as an energy source, so it does not actually need additional heating. Photoreforming always produces hydrogen, so the type of plastic doesn’t matter so much, although certain types of plastic are more readily degraded than others. Contamination on the plastics is not a problem, because the contaminants are similarly photoreformed to hydrogen. In a previous study, we have demonstrated photoreforming of other types of waste, meaning that this method is suitable for mixed waste.”
Kuehnel clarifies that his team’s aim is “not to replace conventional recycling”. Instead, they think of photoreforming as “an ideal complementary method” to deal with mixed waste, which is too difficult to separate and therefore ends up in landfills or the oceans.
So, could cars eventually run on carrier bags? “All plastics are energy-rich materials,” Kuehnel says. “They are mostly produced from petrochemicals, and common plastics such as polyethylene and polypropylene are hydrocarbons with a chemical structure similar to petrol. The problem is that we need better means to extract the contained energy from the plastic. Our work currently is at the proof of concept stage, meaning we can generate only small amounts of hydrogen. For polyethylene terephthalate [PET], we are producing 10mg hydrogen from 1g PET, so for filling the tank of a hydrogen car, which is around 5kg, we would need 500kg of plastic waste.”
Kuehnel adds: “We are working on the scale-up at the moment with good results, but it will take some time, perhaps five to ten years, for this to be a commercial process that can compete with cheap hydrogen produced from fossil fuel reforming. We are also developing new materials with better performance and lower toxicity than cadmium sulfide, which is a very important step for a large-scale implementation. The Austrian petrochemical company OMV is supporting our scale-up activities.”
While a time-traveling, flying DeLorean might be a bridge too far, then, it seems Back to the Future’s foresight of energy from rubbish was not so far-fetched. But, as Peel and Kuehnel recognise, an innovation can’t be adopted overnight. Both policymakers and the public have a part to play in the future of recycling. “We need to drive the circular economy for plastics,” Peel says, “which means that we only need resources once to generate plastic products and then plastic waste, the end-of-life product, is converted back into materials to be fed back into the process.”
The issue of plastic pollution has caught the public’s attention with harrowing documentaries such as David Attenborough’s Blue Planet putting the spotlight on the scale of the problem for the planet’s oceans and wildlife. “Any government policy,” Peel recommends, “should reflect these environmental concerns” with investment in chemical recycling and changes to the infrastructure so that there is better separation and sorting of plastic waste. “Plastic Energy has proved the concept with its plants in Spain, so those responsible for regulation and infrastructure [elsewhere] now need to catch up.”