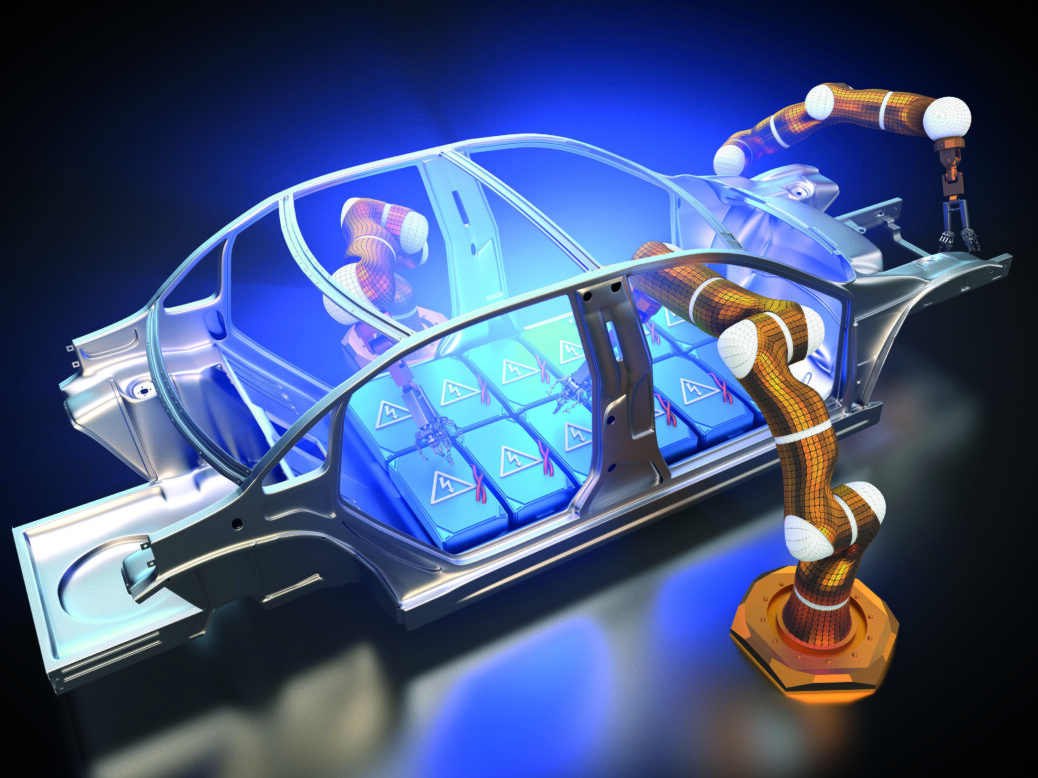
Technological advancement comes at a price. In the context of materials, there is ever increasing demand which is often accompanied by limited supply. Additionally, the raw materials that underpin our modern lives come with environmental and social impacts at many stages in the supply chain.
Critical materials or elements are those which are at risk of short supply but are economically important, including those that possess unique magnetic, catalytic and luminescent properties. Such is the critical nature of these materials to the technologies that enable wind turbines, electric vehicles, fuel cells, electronics and solar panels to name but a few examples, that the European Commission has compiled and regularly updates a list of critical materials, and rare earths are at the top of the list in terms of supply risk. These include dysprosium, neodymium, terbium, europium and yttrium. Rare earth metals are not the only challenge though; platinum group metals are required as catalysts in electrolysers, fuel cells and pharmaceuticals synthesis, and cobalt remains a key component of electric vehicle batteries.
Dr Paul Anderson of the University of Birmingham’s School of Chemistry explains: “It’s important to understand that, despite the name, many critical materials are not ‘rare’ because of a lack of abundance in the earth’s crust. Supply constraints may arise because resources are subject to political interference or manipulation of the market, because they are cheaper to produce in other countries that may be willing to pay an environmental penalty, or because of political instability, for example so-called ‘conflict minerals’. In many cases these materials are not produced on a massive scale so the mining market is small in relative terms, but the products they go into have enormous societal and economic value. They are also frequently very finely dispersed in the applications they are used in which causes problems for recycling.”
Diversifying the supply options for critical materials, developing substitutes and enabling the recycling of end-of-life electrical products, then, should be key priorities for government, academia and industry moving forward. And these represent the core tenets of the University of Birmingham’s Centre for Strategic Elements and Critical Materials (BCSECM).
Rare earth magnets, based upon an alloy of neodymium-iron-boron, play a crucial role in thousands of products. The magnets are used in motors, generators, fans and power steering units in electric vehicles, and are therefore a key resource as the automotive industry transitions to manufacturing ever greater volumes of electric and fuel cell vehicles. For a new generation of off-shore wind turbines, up to three tonnes of NdFeB can be required. The next generation of electric aircraft will also require even greater quantities of these materials.
While it remains possible for engineers to design rare earths out of motors and generators, this will typically be at the expense of efficiency, increased weight or reduced reliability, which will have a negative impact overall on greenhouse gas emissions.
Professor Allan Walton of Birmingham’s School of Metallurgy and Materials says: “Presently, China has a dominant position in the supply of material for rare earth magnets; this provides them with a competitive advantage that allows Chinese manufacturers to move up the supply chain through cost-effective access to critical resources. With a near monopoly on supply and high global demand, the price of rare earth magnet material has gone through periods of extreme price volatility, which could easily occur again in the near future.”
Walton continues: “For a robust economy that considers materials security as part of a proactive industrial strategy, it is essential for the UK to have a diverse range of supply options for critical materials. One of these options could involve developing technologies to recycle critical materials from end-of-life technologies. It has been estimated that every year we import around 14,000 tonnes of NdFeB into the EU. However, there are technical, legal and economic barriers which have to be addressed to make this a reality. Workers at the University of Birmingham are currently scaling up recycling technologies to recover NdFeB magnets from electronic and automotive waste.”
By developing secondary sources of critical materials and by investing in ethical primary resources this can help mitigate the often serious social and environmental costs of mining in many parts of the globe. For example cobalt, a metal with significant supply risks, is subject to growing demand owing to our appetite for lithium ion batteries.
Our present primary supply routes for cobalt raise many moral and ethical questions, with a large proportion being extracted in unsafe conditions by artisanal and often child miners in the Democratic Republic of Congo. The University of Birmingham is leading an EPSRC-funded project on recycling of lithium ion batteries (ReLiB), one of four “fast start” projects launched by the Faraday Institution earlier this year. Birmingham is leading a consortium of eight universities that is investigating how electric vehicle batteries can be economically and safely recycled at the end of their lives.
As the volume of EVs on the road increases, this challenge will only increase. It should be noted that secondary supplies will only ever meet part of the demand in a growing market and we should also be looking to secure supplies of materials in politically stable parts of the world where possible.
Following the launch of the BCSECM, the Centre has subsequently been awarded funding from the EPSRC to launch the Critical Elements & Materials (CrEAM) network. The network will bring together researchers from across the academic landscape with the aim of informing and safeguarding UK industry against shortages of critical materials. Later in 2018, the BCSECM will also launch a policy commission, examining the potential for a dedicated “UK Elements Strategy”. At a time when politics and policy are uncertain – a backdrop exacerbated by the UK’s impending exit from the European Union – it is important to consider carefully our position in relation to critical materials in a totally new context. This is essential to ensure that UK industry remains competitive globally and key resources are available at the right price to our manufacturers.
A bespoke UK Elements Strategy, modelled on the long-standing Japanese equivalent which is based on a hierarchy of replace, reduce, recycle, regulate, could provide proactive policy guidance to mitigate potential price and geopolitical volatility in relation to strategic and critical elements.
Dr Gavin Harper is the Energy Development Manager at the University of Birmingham.