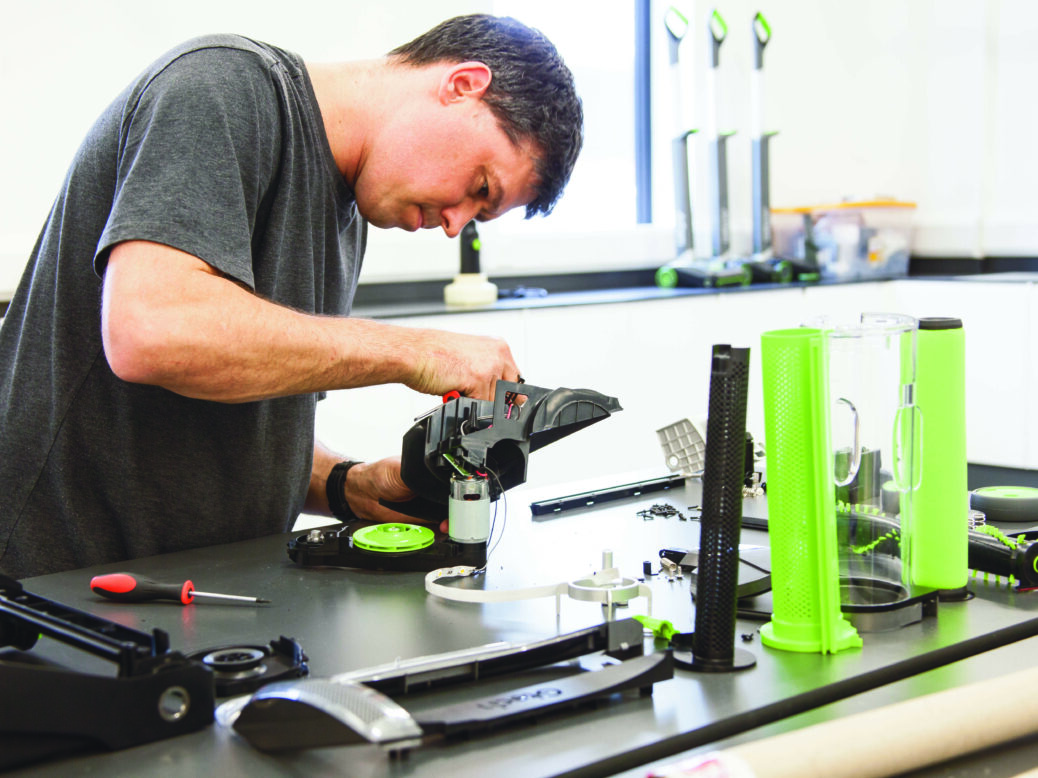
“I didn’t really get on well at school,” recalls Nick Grey. “I didn’t like it, and it didn’t like me very much”. Work, however, was a different matter. In his first job in the design lab at vacuum cleaner company Vax, Grey found that “design was something I found really easy. It came quite naturally.” From a lab technician Grey became a design engineer and eventually, in his early 30s, the company’s head of engineering and design. He left Vax in 2001 with enough savings to last him a year or so, a home office in a village outside Worcester, and an idea for a new company. Less than 15 years later he had sold tens of millions of products in countries around the world, and last year the company, which remains 90 per cent owned by Grey and his family, turned over £91m.
For those with an eye on British manufacturing, then, it was encouraging to hear that this burgeoning company (Gtech was named the fastest-growing company in the Midlands in 2016, and the 11th fastest-growing in the UK) plans to make its next vacuum cleaner in Britain.
“It’ll create 100 jobs,” says Grey. “About half of them will relate directly to manufacturing and half will be related positions, such as admin and customer service.”
Why manufacture in the UK? “People want to use British products. They are always very complementary about Gtech and what we do, but the one thing people say is, ‘why don’t you manufacture here?’ So we designed a product specifically for British manufacture.”
Grey says this is not simply a case of moving a product line from China back to Britain; the economics of manufacturing in the two countries are different, and this changes how products are designed. “You can’t build things that are hugely labour-intensive in the UK – it just isn’t competitive. But if you make it relatively straightforward to put together, and find some savings elsewhere, it should work.”
“I think there’s a lot of pride that we can manufacture our own stuff, still. When you manufacture a product anywhere, it’s usually made from raw materials or parts that are brought in. But being able to manufacture here, being able to say we can compete, you can build a product in Worcester and it can compete with products built anywhere – I think there’s a lot of pride in that.”
The environmental benefits, too, are a selling point. Shipping already releases a billion tonnes of CO2 into the atmosphere each year – more than three times the UK’s total emissions – and this could rise to 17 per cent of total world emissions by 2050. Many consumers already avoid food from the other side of the world; product manufacturers may soon need to consider this as a force in buying decisions.
For Grey these efficiencies are what bring UK manufacturing “within touching distance of the price of manufacturing offshore.” “We’ll save a lot of shipping costs, we’ll save storage costs, and we’ll save picking and packing costs.” When the new vacuum gets to the end of the production line in Worcester, he says it will go “straight onto the courier’s van to go out to consumers. That helps make up for the higher cost of manufacturing here.”
The sum that has to be balanced for a company to be able to manufacture in the UK rather than China is weighted heavily towards the east. While Chinese workers’ wages have risen dramatically in recent years, the average wage in manufacturing remains around £2.60 to the UK’s £8.20. In factories in Sri Lanka and Bangladesh, where many of the clothes worn in the UK are made, workers are typically paid £2-£4 a day. Factory space is also much cheaper and more readily available abroad. In the UK, says Grey, “there’s a shortage of space. Manufacturing needs a lot of space, and the rent and the rates are very expensive here. It can actually be difficult to find factory space even if you’ve got the money.” When Gtech left its old office – a collection of buildings on a farm – in 2016, Grey says that “on the local property pages, there were two properties of the right size within the limits of Worcester. The whole choice was two properties. One of them was very old and run down, and the other was the one we moved into.”
Grey says that factories in China also benefit from a government that actively promotes manufacturing. “The investment in China is readily available. For any factory that wants to export goods, they can borrow money, open premises, buy machinery, and the government is very, very supportive. Here, you basically have to have a lot of money.”
This situation is not new. Grey describes manufacturing in the Far East as “very mature” in terms of the quality of manufacturing, and the availability of skilled workers is “like for like”. “We’re able to attract a very strong workforce here too,” he adds, but the higher value placed on a UK citizen’s time means products must be designed accordingly. “You need something that’s fairly streamlined in its design and assembly.”
That said, Grey acknowledges that the UK government does offer some “very good” incentives for businesses. He highlights research and development tax relief – a considerable deduction from corporation tax that can be claimed whether R&D is successful or not – as a policy that strongly incentivises innovative companies such as Gtech.
This is good for the UK because “most of the value of a new, innovative product is in the intellectual property,” he says, pointing out that manufacturing in the UK doesn’t actually bring in as much value as designing in the UK. “That’s the really important bit. Britain has this incredible resource of design talent, from Spitfires to radar to F1 cars – the very top of design is usually British influenced. So to make the most of that is the main thing for government. Research, development and design, that’s what we’re good at.”
In the US, Donald Trump’s promise during his election campaign to “get Apple to start making their computers and their iPhones on our land, not in China,” shows a failure to understand the realities of globalised business and manufacturing. According to Grey, “anything that’s compact, labour-intensive and easy to ship, you’re better off making in the Far East. If it’s quite bulky and big, or if it’s not labour-intensive, you’ve got a chance, you can manufacture that locally.”
“I would encourage British manufacturing,” he says, “just not of everything.”
The decision to manufacture in the UK could also represent a Brexit insurance policy for Gtech. Following the referendum, the cost of materials – which are for Gtech negotiated in US dollars – rose steeply as the pound lost value. “It certainly wiped some off our bottom line,” says Grey, agreeing that reshoring “does underpin that a little bit.” That said, Grey points out that EU law has made “selling goods within the EU more complicated than selling them outside, “so Brexit “doesn’t make any difference to us, to be honest.”
The new Gtech model, when it begins production later this year, will not be the only vacuum cleaner made in the UK (Numatic has made its well-known Henry vacuum in Somerset for more than 35 years) but it will be an important test of British manufacturing’s appeal to consumers in the modern economy. If it is successful, other companies may find both efficiency and security following Gtech’s lead.